工場勤務なんだけど、改善提案がネタ切れ…
って、工場勤務の「あるある」ですよね。
私も工場勤務が長いので、何度も、改善提案が思いつかなくて、その結果ネタ切れになったことがあります。
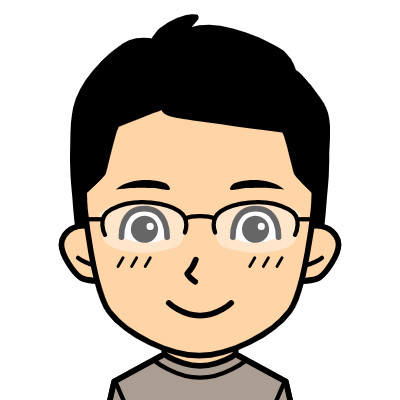
上司や同僚に改善提案が思いつかないから相談しても、そっけない場合が多いんです。
「自分で考えて~」って感じで軽くあしらわれます。
なので、工場で改善活動があるたびに、
「ああ、また改善提案か…思いつかない」
ってなって、ちょっとストレスに感じてしまっていたんです。
ですが、トヨタ自動車のシート製造の工場で出会った上司は、ちょっと違っていたんですよ!
その上司は、
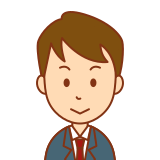
改善案って、全然思いつかななくてネタ切れになってしまうことが多いよね。
そんな時は、「5S」と「3M」とあと1つネタがあるから、それを軸に考えたらいいよ!
って感じで、改善提案のアイデアのコツを教えてもらいましたよ~。
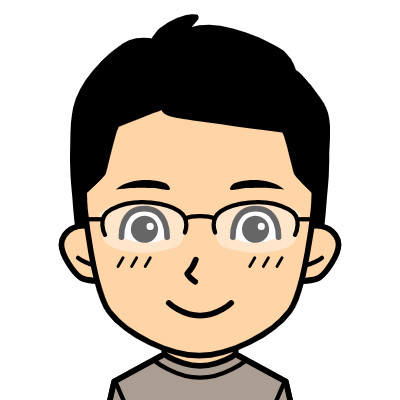
トヨタ自動車のシート製造の工場の上司に感謝!
その結果、それからは、改善提案にあまり悩まなくなりました。
スルスルとスムーズに改善提案のアイデアが思いつくわけではありませんが、その逆に「ネタ切れ…」といったこともなくなりました。
時間はかかりますが、改善提案のネタはちゃんと提出することができ、その結果、部署の活動に貢献できていたと思います。
ということで本日の記事は、工場勤務で改善提案がネタ切れ…ってお悩みのあなたのために、アイデアを出すコツについて、わかりやすく紹介していきますね~。
工場勤務で改善提案がネタ切れにならないための対処法
工場勤務をしているひとであればわかると思いますが、部署の活動として、「改善提案」を定期的に求められますよね。
あれって、最初の頃は、必死に考えて改善提案のアイデアを提出するのですが、何度もやっていると、
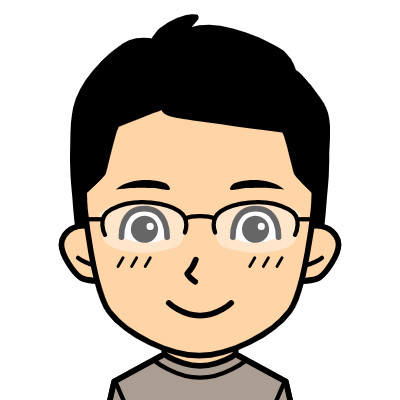
もうアイデア切れかな…なにも思いつかない
ってなってしまうこともあります。
そんな時に、思い出してほしいことは、工場作業の基本である
・3M
・5S
・情報の見える化
なんです。
これを軸に考えていくのですが…考え方にもコツがあるんですよ!
といってもむずかしくないですよ~。
これを読んでいただければ、すぐに思いつく…というか、実行することができます。
ということで、さっそく紹介していきますね~。
改善提案の「3M」とは?
まず最初に、3Mについて紹介していきます。
といっても、これは有名だから知っている人も多いんじゃないかな。
3Mとは、
・無理
・無駄
・ムラ
の3つのことです。
この3つをざっくりと解説すると、
・無理:作業員の能力よりも作業量が多いこと
・無駄:作業量よりも作業員の方が多いこと
・ムラ:作業量(作業員)にばらつきがあること
となります。
無理:作業員の能力の限界値よりも作業量が多いと、
・作業員に負担がかかる
・残業が増える
といったデメリットにつながります。
無駄:またその逆に、作業量よりも作業員の方が多いと、
・作業員が遊んでしまう
・人的コストがかかる
となってしまい、これまた会社にとっては良いことがないですよね。
ムラ:さらに言うと、作業員と作業量にばらつきがあると、生産にもばらつきが出てしまうので、その結果、他のスケジュールを圧迫してしまうことも考えられます。
なので、工場としては、この3M
・無理:作業員の能力よりも作業量が多いこと
・無駄:作業量よりも作業員の方が多いこと
・ムラ:作業量(作業員)にばらつきがあること
に関しては、なるべくなくそうと改善している場合が多いですね。
次に、5Sについて紹介していきますね~。
改善提案の「5S]とは?
次に、改善提案における「5S」についても紹介していきます。
と言ってもこれも有名なので、知っている人も多いともいます。
「5S」とは…
・整理
・整頓
・清掃
・清潔
・しつけ
の頭文字をとって5Sと言います。
整理整頓って案外できていない場合が多いんですよ。
わかりやすく言うと、
・ほうき
・ちり取り
の置いてある場所が違う…なんてベタな具体例ですが、結構わかりやすいですよね。
こんな感じで、
・ねじ
・ドライバー
とか
・釘
・ハンマー
とか
・サンダー
・替え刃
とか、
・エアーガン(ノズル)
・エアホース
などセットで使うものが違う場所で管理されていると、ちょっと使いにくいですよね…。
なので、こういったものをまとめて管理するのも、整理/整頓の改善提案につながりますよ~。
また、清掃に関しては、これは次に紹介する「情報の見える化」と一緒に考える場合が多かったので、その事例を次で紹介していきますね~。
情報の見える化
「情報の見える化」って最近よく言われますよね。
これって、とても重要なんですよ!
例えば、
・月(週)の生産状況
・生産完了品の在庫量
・生産スケジュール
などは、情報の見える化が進んでいて、今では、パソコンからリアルタイムで見ることができる工場もあります。
この「情報のみえる化」ですが、実は生産に関するものだけじゃなくてもいいんですよ。
例えば、
・危険個所のアナウンス
・在庫のアナウンス
・点検の書き込み
などなど…いろいろな場所に使うことができます。
例えば先ほど紹介した5Sの「清掃」に関しても、工場内では、
・1日に1回
・1週間に1回
・月に1回
といった感じで、場所によっては、「汚い場所」と、その逆に「きれいな場所」で温度差がありますので、それに対応した清掃頻度になります。
ですが、「週に1回」とか「月に1回」の清掃…となると、次の期間までが長いので、
・誰がやるのか?
・どの班がるのか?
が、イマイチ他人任せになってしまうことが考えられます。
なので、「掃除のチェックシート」を作成することで、
・5Sにもつながるし
・清掃状況を把握できるし
・次にいつやればいいのか?が簡単にわかる
といった感じで、これは結構使える事例だと思います。
また、この「情報の見える化」ですが、在庫不足の対処法としても使用できます。
例えば、
・釘
・ねじ
といったものって、工場ではみんながよく使うので、「誰が発注したのか?」がよくわからない場合が多いと思います。
なので、具体的な事例として…
釘の箱がいてある棚に「在庫が半分になったら、発注すること。発注した場合には、「発注済みのカードを表示」なんてシステムを作って、それを貼っておくことで、在庫の管理がとても楽になります。
この場合は、「整理/整頓+情報の見える化」の事例として、わかりやすいかな。
こんな感じで、
・3M
・5S
・情報の見える化
を単体で考えると、アイデアとしては思い浮かばない場合が多いですが、それをうまくつなぎ合わせることで、改善提案のいいアイデアが生まれます。
ということで次に、具体的な事例を紹介していきますね~。
工場の改善提案の具体例3つ
ということで、工場における具体的な改善提案の事例について、3つ細紹介していきます。
まず最初は、「3M+情報の見える化」の事例です。
「3M+情報の見える化」の改善事例
以前勤めていた工場ですが、この工場は、作業員が少ない職場でした。
なので、ベテランさんが作業量の多い部署に来て、手伝ってもらうこともしばしばありました。
具体的に言うと、
・生産は順調
・だけど、梱包の人が足りない
って感じで、人が少ない時は生産の部署の人に応援に来てもらうことが度々あったんですよ。
これって、人を増やすのが一番いい解決策ですが、でもそれってなかなかスムーズにいかないですよね。
なので、梱包の在庫の状況のデータを、生産の部署と共有することにしました。
これって情報の見える化ですよね!
梱包の状況を、手伝いに来てくれる生産の部署と共有することで、
・梱包がどれだけ遅れているか?が一目でわかる
・手伝いに来てくれる人のタイミングもつかめる
・手伝えるおおよその時間が計算できる
といった感じで、その後は、割とスムーズにいくようになりましたよ~。
自分の働いている部署と、そのほかの部署って、交流があまりないと、なかなか情報共有できない場合が多いですが、そのせいでスムーズにいかないこともあるんですよ。
(その結果、無理/無駄/ムラ、につながります)
なので、そういったことを防いでスムーズに作業をこなすためにも、情報の見える化をして、効率化を図ってください。
次に「5S+情報のみえる化」の事例について紹介していきますね
「5S+情報のみえる化」の改善事例
先ほども書いたように、
・清掃の情報の見える化(チェックシート)
・在庫の見える化(発注状況の把握)
なども、5S+情報の見える化ですが、これ以外だと、
・定期点検の情報の見える化
・グリスアップの情報の見える化
・オイル交換の情報の見える化
なども具体例として使えますよね。
ですが、もっと基本の「ごみ箱の見える化」をやった時は、結構好評でしたよ~。
具体的に書くと、
・ゴミ箱の8分目くらいの場所に線を引く
・そこに「この部分までたまったら捨てる」と書く
・替えのごみ袋を隣に用意しておく
と、たったこれだけ!
ごみ箱って、できているようで案外できていないパターンが多いと思います。
(その結果、ごみ箱はいつも満タン…じゃないでしょうか?)
なので、
・基準となる線を引いて
・それを超えたら捨てに行く
といった方式でやってったらいいと思います。
※ごみ箱の場合、「週に1回金曜日は捨てに行く」って決めるのもいいですが、それだと、
・少ない時は捨てにいかない
・金曜日よりも前にいっぱいになっても捨てに行かない
といった感じで、「曜日を決めて…」といったやり方は不評でしたので、あわせておぼえておいてください。
最後に、KY(危険予知)と情報の見える化を合わせた改善事例を紹介していきますね~。
KY(危険予知)と情報の見える化を合わせた改善事例
工場勤務の場合、KY(危険予知)活動を知らない人はいないと思います。
ケガをしないために、
・危険な場所
・危険なタイミング
・危険な行動
を知って、それを防ぐ活動ですが…これを「情報の見える化」と組み合わせることでも改善提案活動になります。
私が実際にやったことは、「標識を立てる事」です。
といってもA4の紙に
・頭上注意
・足元注意
・フォークリフト注意
・温度注意(高温注意)
みたいな感じでプリントして、それを当てはまる場所に貼るだけ!
特に工場の場合、設備のレイアウトによっては、
・設備の下をくぐったり
・設備の上を渡ったり
といった感じで、危険な個所がたくさんあります。
そこに「〇〇注意!」という張り紙を貼るだけですので、簡単にできますので改善提案のネタが切れてしまった場合は、これをよく使っていました。
さいごに…
工場勤務の場合、他の工場で起こった事故の事例などを定期的に目にすると思います。
そう言った情報も参考にすることで、改善提案のネタ切れは結構減るんじゃないかな。
工場って日々改善されて、改善活動においては、なかなかたらしいアイデアが出にくいとは思いますが、頑張ってください。
本日の記事は以上です。
最後までお付き合いいただき、ありがとうございます。
コメント